Exploring BPM Top Drive Setup: Electrical and Control Systems Guide with SINAMICS S120 Drive
In the world of drilling, top drive systems have changed the game. I've had the chance to work with many types, but recently on a new rig, I've been using the BPM top drive, specifically the DQ70BSD-D model. It's manufactured by Beijing Petroleum Machinery Co. and it's becoming quite popular because it's strong and has some cool features. In this article, I'm going to talk about what powers the BPM top drive, especially its electrical parts like the Variable Frequency Drive (VFD), the PLC, and how it all works together. I’ll share what I've learned from using this system myself, and I'll try to explain how it fits into today's drilling world, what makes it work so well, and how it makes a difference.
Keep in mind that what I describe might be a bit different from other rigs because not all setups are the same.
Overview of the Electrical System
The BPM Top Drive is equipped with a sophisticated electrical control system designed to optimize performance, safety, and efficiency in drilling operations. This system is primarily composed of three critical components: the Variable Frequency Drive (VFD) system, the PLC/MCC system, and the necessary associated cabling.
Variable Frequency Drive (VFD) System:
The VFD system is a pivotal component of the top drive, utilizing Siemens SINAMICS S120 Drives. This setup includes:
Line Connection Module (LCM)
Basic Line Module (BLM)
Motor Operator Module (MOM)
Braking resistor
For more in-depth look at VFDs, you can check out my article on The Fundamentals of Variable Frequency Drives: Understanding Motor Speed Control
PLC/MCC System
At the heart of the electrical control is the PLC/MCC system, comprising:
PLC/MCC cabinet
Driller’s Console
Local Control Box mounted on the Top Drive's main body
Power Structure
The electrical power structure of the BPM begins with 600V AC power transmitted from the generator to the Top Drive's Electric House. Here, it undergoes rectification to 810 VDC via a line reactor and BLM for the DC bus. The MOM then utilizes this power to provide three-phase variable frequency current using the PWM method for precise control.
Auxiliary power needs are met through transformers stepping down the voltage to 460V and 220V for various components, while SITOP Modules convert AC 220V to DC 24V for control elements.
Communication Structure
The system uses Siemens SIMATIC S7-1500 PLC modules for its central PLC, which guarantees strong and effective management of the processes. It communicates via a network that utilizes fiber optics for connecting to the Local Control Box and Profinet cables to link up with the Driller's Console
VFD Structure
The Variable Frequency Drive (VFD) is a crucial component of the BPM Top Drive, enabling precise control over the main motor's speed and torque.VFD on BPM system consists of 5 essential components:
1-Line Connection Module (LCM)
The LCM serves as the frontline of the VFD system, providing power to the BLM. It is equipped with a main air switch and a line reactor to stabilize the power supply and protect the system. Additionally, a Multifunction power meter is installed within this cabinet to monitor and manage power distribution effectively.
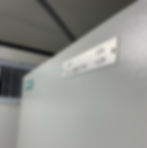
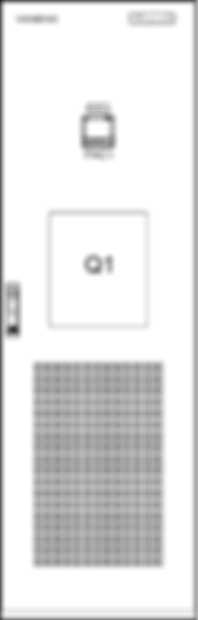
2- Basic Line Module (BLM)
The BLM is responsible for rectifying the 600V AC power received from the LCM into 810 VDC, supplying power to the DC bus.


3- Motor Operator Module (MOM)
The MOM cabinet, connected to the DC bus converts the stable DC power back into variable frequency AC power, controlling the speed and torque of the main motor.

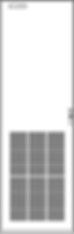
4- Controller and Communication
The operation of BLM and MOM is coordinated by the CU controller located in the PLC/MCC cabinet. Communication between the controller and these modules is facilitated through the DRIVE-CLiQ protocol (an Ethernet-based protocol from Siemens that interfaces with SINAMICS control systems), ensuring efficient and reliable transmission of control signals.
5- Braking Unit
An integral part of the BLM, the Braking Unit module is linked to the DC bus and connected to the braking resistor housed in the electric house. In moments where rapid deceleration is needed, the braking unit dissipates the electrical energy as heat through the braking resistor.

PLC System
The Programmable Logic Controller (PLC) system of the BPM Top Drive is the brain behind its operations, providing precise control and monitoring capabilities that are integral for the rigorous demands of drilling. The system consists of a PLC/MCC cabinet, a Local Control Box (LCB), and the Driller's Console (TCC). Each component plays a critical role in the overall functionality of the Top Drive.
1- PLC/MCC Cabinet

The PLC/MCC cabinet is the central hub, housing an industrial PC (IPC), PLC Modules, Drive-controller, and various terminals. It's equipped with numerous indicators and manual switches for comprehensive control and status monitoring.
Indication elements:
IBOP DISABLE:Â Lights up to indicate that the Inside Blowout Preventer (IBOP) function is disabled,
PHASE MONITOR:Â This indicator is active when the power supply's phase sequence is correct, ensuring that the electrical system is receiving power in the proper orientation for safe operation.
Encoder fault:Â Illuminates when the system is operating without the encoder feedback, suggesting a potential issue or a bypass mode where encoder input is not being used.
Motor HEATING:Â Shows that the heating element for the main motor is active
HYD RUNNING:Â Indicates that the Hydraulic Power Unit's (HPU) pump motor is running, providing the hydraulic flow necessary for the top drive's operations.
Power ON:Â This light is on when the main air switch is closed, signifying that the cabinet is energized and ready for operation.
System Ready:Â Signifies that the VFD is ready to drive the main motor. It flashes when the system start command is given but the VFD is not ready to proceed
Fault/Alarm:Â A flashing light signals an alarm condition, while a steady light indicates a fault has been detected, requiring immediate attention.
BUZZER: Sound Warning for alarm or fault
Manual Key switches:
Encoder Select Key Switch:Â Allows the operator to choose between encoder signals at models two main motors are present. In single motor configurations, the corresponding motor's encoder should be selected, or it can be set to "Remote" to select the encoder via the HMI.
Control Mode Key Switch:Â Selects the communication status for the local control box. "Profinet" is the default setting for normal operations, while "Cable" can be selected for emergency operations if Profinet is unavailable.
IBOP Disable Key Switch:Â Controls the locked status of the IBOP, preventing accidental closure during special operations. It is switched to "DIS." before operations where IBOP should not be activated and to "EN." when normal drilling resumes.
Encoder Fault Key Switch:Â Set to "Normal" under standard operating conditions, or to "Fault" if there is an issue with the main motor's encoder and operations must continue.
MOTOR HEATER Key Switch:Â Used to manually control the main motor's heating function, with interlocks to prevent operation when the motor is running.
HYD RUNNING Key Switch:Â Manually controls the hydraulic pump, with "ON" for power, "REMOTE" for control via the Driller's Console, and "AUTO" for PLC-based automatic control.
HYD COOLING FAN Key Switch:Â Operates the cooling fan, with settings for "ON," "OFF," and "AUTO" for PLC-controlled operation.
System Start Key Switch:Â Engaged to start the top drive's main shaft, closing the main air switch and energizing the system.
RESET/SILENCE Button:Â Pressed once to silence alarms, or twice to reset alarms or faults, ensuring operators can quickly address and clear any issues.
E. Stop:Â The emergency stop button rapidly halts operations and disconnects the main air switch. All E-Stops are interlocked, so triggering one stops the whole system after a brief delay
Industry PC:
The PC serves as the interface for the HMI, programmed through WinCC Software, allowing for intricate control and system diagnostics

AOP30:
the AOP30 is installed for real-time monitoring and adjustment of inverter parameters.

2- Local Control Box (LCB):
Attached directly to the main body of the Top Drive, the LCB connects control cables and provides power for the main motor’s auxiliary functions like the cooling fan and heater. It is also a central hub for sensor signals, collecting data on temperatures, lubrication, and vibration status to ensure optimal performance and safety.

Driller's Console (TCC)
The Driller's Console is the driller's primary interface with the Top Drive, enabling control and monitoring of its functions. The console features a range of operation elements, including switches for the rotating head, clamp, and IBOP, as well as hand wheels for speed and torque settings. The touch panel allows for setting adjustments and parameter monitoring, ensuring the driller has full command over the Top Drive's operations.

Protection Limits in Drilling operations
The BPM Top Drive features an advanced protection system designed to mitigate risks and preserve the longevity of its components. Here we explore the key protection limits that are instrumental in maintaining safe drilling operations:
Torque Limiting: The system is programmed to respond when the actual drilling torque reaches the preset value entered by the operator. Upon reaching this threshold, the main shaft will cease rotation (speed = zero), effectively stopping drilling while maintaining the torque level. If the torque subsequently decreases, the system will resume rotation at the preset speed, ensuring consistent drilling performance without overexerting the equipment.
Motor Temperature Alarm: High motor temperatures trigger an automatic response from the system. To prevent overheating, the main shaft's speed is restricted to 60 rpm or less.
Blower Fault Alarm: A blower fault alarm activates a similar protective response. The system automatically limits the main shaft's speed to 60 rpm or less.
Gearbox Lubrication Alarm: Lubrication issues within the gearbox are a serious concern and prompt the system to half the preset value of speed setting
Gearbox Oil Temperature Alarm: Overheating of the gearbox oil enacts a speed limitation where the main shaft is restricted to 60 rpm or less.
As we conclude this exploration of the BPM Top Drive, it's important to remember that while setups may vary across different rigs, the principles of operation remain constant. Whether you are directly involved in the drilling industry as an electrical engineer on a drilling rig or simply interested in reading about this technology, I hope this article has provided valuable insights into the world of top drive systems. If you have any inquiries or comments, or if you wish to discuss this technology further, please feel free to contact me. Your thoughts and curiosities are always welcome, and I look forward to engaging in further discussions on this and related topics.